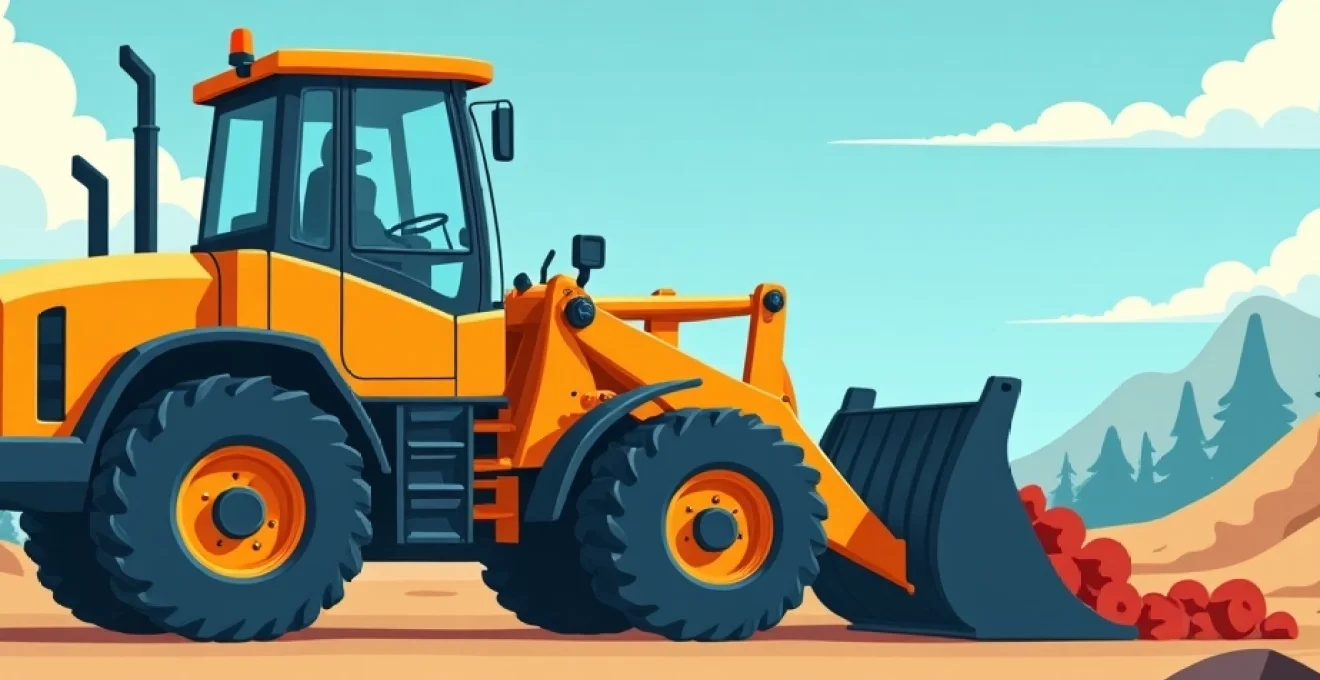
La sécurité et la longévité des engins de chantier sont des priorités cruciales dans l'industrie de la construction. Avec l'évolution rapide des technologies, de nouvelles solutions émergent pour protéger ces machines coûteuses et vitales. Des systèmes anti-collision avancés aux matériaux de pointe pour le renforcement structurel, en passant par la maintenance préventive intelligente, les innovations ne cessent de repousser les limites de la protection des engins. Cette approche globale de la sécurité ne se limite pas à l'équipement lui-même, mais s'étend également à la formation des opérateurs, créant ainsi un environnement de travail plus sûr et plus efficace.
Sélection des accessoires de protection pour engins de chantier
Le choix judicieux d'accessoires de protection est essentiel pour préserver les engins de chantier des dommages potentiels. Ces équipements spécialisés agissent comme une armure, protégeant les parties vulnérables des machines contre les impacts, l'usure excessive et les conditions environnementales difficiles. Parmi les accessoires les plus couramment utilisés, on trouve les plaques de protection pour le dessous de caisse, les grilles de protection pour les vitres, et les renforts pour les godets et les bras articulés.
Les plaques de protection sous caisse sont particulièrement importantes pour les engins travaillant sur des terrains accidentés. Elles préviennent les dommages aux composants vitaux comme le moteur, la transmission et les réservoirs de carburant. Ces plaques sont généralement fabriquées en acier haute résistance ou en alliages d'aluminium pour offrir une protection maximale sans ajouter un poids excessif à la machine.
Les grilles de protection pour les vitres sont un autre accessoire crucial, notamment pour les pelles mécaniques et les bulldozers opérant dans des environnements où des débris peuvent être projetés. Ces grilles, souvent en acier ou en polycarbonate résistant aux chocs, protègent non seulement les vitres coûteuses mais aussi, et surtout, la sécurité de l'opérateur.
Pour les engins équipés de bras articulés et de godets, des renforts spéciaux peuvent être installés pour augmenter leur durabilité. Ces renforts sont conçus pour résister à l'abrasion intense et aux chocs répétés, prolongeant ainsi considérablement la durée de vie de ces composants soumis à rude épreuve.
Systèmes anti-collision avancés pour engins lourds
Les systèmes anti-collision représentent une avancée majeure dans la prévention des accidents sur les chantiers. Ces technologies sophistiquées utilisent une combinaison de capteurs, de caméras et de logiciels pour créer un bouclier virtuel autour de l'engin, alertant l'opérateur des dangers potentiels et, dans certains cas, intervenant directement pour éviter une collision.
Radars de recul et caméras 360° pour visibilité optimale
Les radars de recul et les caméras 360° sont devenus des équipements standard sur de nombreux engins de chantier modernes. Ces dispositifs offrent une visibilité complète de l'environnement de travail, éliminant pratiquement les angles morts qui sont souvent à l'origine d'accidents graves.
Les radars de recul utilisent des ondes sonores pour détecter les obstacles et alerter l'opérateur par des signaux sonores et visuels. Leur efficacité est particulièrement appréciée dans des conditions de faible visibilité, comme la nuit ou par mauvais temps. Les caméras 360°, quant à elles, fournissent une vue panoramique de l'environnement immédiat de l'engin, affichée sur un écran dans la cabine. Cette technologie permet à l'opérateur de visualiser en temps réel tout ce qui se passe autour de la machine, réduisant considérablement les risques de collision.
Dispositifs d'alerte de proximité par ultrasons
Les dispositifs d'alerte de proximité par ultrasons constituent une couche supplémentaire de protection contre les collisions. Ces systèmes émettent des ondes ultrasonores qui rebondissent sur les objets environnants, permettant de détecter avec précision la présence et la distance des obstacles.
Lorsqu'un objet ou une personne s'approche trop près de l'engin, le système déclenche une alerte, généralement sous forme de signal sonore et visuel dans la cabine. Certains systèmes plus avancés peuvent même activer automatiquement les freins de l'engin si la distance critique est atteinte, offrant ainsi une protection supplémentaire contre les erreurs humaines.
Intelligence artificielle et apprentissage automatique dans la prévention des collisions
L'intégration de l'intelligence artificielle (IA) et de l'apprentissage automatique dans les systèmes anti-collision représente la prochaine frontière de la sécurité des engins de chantier. Ces technologies avancées permettent aux systèmes de s'adapter dynamiquement à leur environnement et d'anticiper les dangers potentiels avec une précision croissante au fil du temps.
Les algorithmes d'IA analysent en temps réel les données provenant de multiples capteurs, caméras et radars, créant une compréhension contextuelle de l'environnement de travail. Cette analyse permet au système de distinguer entre différents types d'obstacles, d'évaluer leur niveau de risque et de prédire leurs mouvements potentiels. Par exemple, un système basé sur l'IA peut différencier un travailleur en mouvement d'un objet stationnaire et ajuster ses alertes en conséquence.
L'apprentissage automatique permet à ces systèmes de s'améliorer continuellement en apprenant des situations passées. Chaque chantier, avec ses défis uniques, contribue à affiner les algorithmes, rendant le système plus efficace et plus précis dans la détection et la prévention des collisions.
Renforcement structurel des cabines et châssis
Le renforcement structurel des cabines et des châssis est un aspect crucial de la protection des engins de chantier et de leurs opérateurs. Ces améliorations visent à augmenter la résistance de la machine aux impacts et aux retournements, deux des dangers les plus sérieux sur les chantiers.
Matériaux composites haute résistance pour cabines ROPS et FOPS
Les structures de protection contre le retournement (ROPS - Roll-Over Protective Structures) et les structures de protection contre les chutes d'objets (FOPS - Falling Object Protective Structures) sont essentielles pour la sécurité des opérateurs. Traditionnellement fabriquées en acier, ces structures bénéficient désormais de l'utilisation de matériaux composites haute résistance.
Ces matériaux composites, souvent à base de fibres de carbone ou de kevlar, offrent un rapport résistance/poids nettement supérieur à celui de l'acier traditionnel. Ils permettent de concevoir des cabines plus légères tout en améliorant leur capacité à absorber et à dissiper l'énergie d'un impact. De plus, leur résistance à la corrosion contribue à prolonger la durée de vie de ces structures de protection.
Conception modulaire pour absorption d'énergie en cas d'impact
La conception modulaire des cabines et des châssis représente une approche innovante dans la protection contre les impacts. Cette méthode consiste à créer des zones de déformation programmée qui absorbent et dissipent l'énergie d'un choc de manière contrôlée, préservant ainsi l'intégrité de l'espace de survie de l'opérateur.
Ces structures modulaires sont conçues pour se déformer progressivement lors d'un impact, réduisant les forces transmises à l'opérateur. Les modules peuvent être remplacés individuellement après un accident, ce qui simplifie et réduit le coût des réparations. Cette approche s'inspire des technologies utilisées dans l'industrie automobile, où elle a prouvé son efficacité pour améliorer la sécurité des occupants.
Normes ISO 3471 et ISO 3449 pour la protection contre le retournement
Les normes ISO 3471 et ISO 3449 établissent des critères stricts pour la conception et les tests des structures de protection contre le retournement et les chutes d'objets. Ces normes internationales garantissent que les cabines et les châssis des engins de chantier offrent un niveau de protection adéquat dans des scénarios d'accident réalistes.
La norme ISO 3471 spécifie les exigences de performance pour les ROPS, définissant les forces que la structure doit être capable de supporter sans s'effondrer ou pénétrer dans l'espace de survie de l'opérateur. La norme ISO 3449, quant à elle, établit les critères pour les FOPS, assurant que la cabine peut résister à l'impact d'objets tombants de différentes tailles et énergies.
Les fabricants d'engins de chantier doivent soumettre leurs structures à des tests rigoureux pour obtenir la certification selon ces normes. Ces tests incluent des simulations de retournement et des essais d'impact avec des objets lourds, garantissant que les structures de protection fonctionneront comme prévu dans des situations d'urgence réelles.
La conformité aux normes ISO 3471 et ISO 3449 est devenue un critère de sélection crucial pour les acheteurs d'engins de chantier, reflétant l'importance croissante accordée à la sécurité des opérateurs dans l'industrie de la construction.
Maintenance préventive et systèmes de diagnostic embarqués
La maintenance préventive et les systèmes de diagnostic embarqués jouent un rôle crucial dans la prévention des pannes et la prolongation de la durée de vie des engins de chantier. Ces technologies avancées permettent de détecter les problèmes potentiels avant qu'ils ne deviennent critiques, réduisant ainsi les temps d'arrêt coûteux et les risques d'accidents liés aux défaillances mécaniques.
Capteurs IoT pour surveillance en temps réel de l'état des composants
L'Internet des Objets (IoT) a révolutionné la manière dont les engins de chantier sont surveillés et entretenus. Des capteurs miniaturisés, installés sur les composants critiques de la machine, collectent en permanence des données sur leur état de fonctionnement. Ces capteurs peuvent mesurer une variété de paramètres, tels que la température, la vibration, la pression et l'usure des pièces.
Les données recueillies sont transmises en temps réel à un système central de gestion de flotte, permettant aux gestionnaires de maintenance d'avoir une vue d'ensemble de l'état de santé de chaque engin. Cette surveillance continue permet de détecter rapidement les anomalies et d'intervenir avant qu'une panne ne se produise. Par exemple, un capteur détectant une augmentation anormale de la température d'un moteur peut signaler un problème de refroidissement avant qu'il ne cause des dommages importants.
Analyse prédictive des pannes avec machine learning
L'analyse prédictive, alimentée par des algorithmes de machine learning, pousse la maintenance préventive encore plus loin. En analysant les données historiques et en temps réel provenant des capteurs IoT, ces systèmes peuvent prédire avec une grande précision quand et où une panne est susceptible de se produire.
Les algorithmes de machine learning identifient des modèles et des tendances dans les données qui pourraient échapper à l'œil humain. Ils peuvent, par exemple, reconnaître des combinaisons subtiles de paramètres qui précèdent généralement une défaillance spécifique. Cette capacité de prédiction permet aux équipes de maintenance de planifier les interventions de manière proactive, réduisant ainsi les temps d'arrêt imprévus et optimisant l'utilisation des ressources de maintenance.
Protocoles de maintenance basés sur les données télématiques
Les données télématiques fournissent une vue d'ensemble détaillée de l'utilisation et des performances de chaque engin. Ces informations sont utilisées pour établir des protocoles de maintenance personnalisés , adaptés aux conditions réelles d'utilisation de chaque machine.
Au lieu de suivre un calendrier de maintenance fixe basé sur le temps ou le kilométrage, les protocoles basés sur les données télématiques prennent en compte l'intensité réelle de l'utilisation de l'engin, les conditions environnementales dans lesquelles il opère, et son historique de performance. Cette approche permet d'optimiser les intervalles de maintenance, assurant que chaque intervention est effectuée au moment le plus opportun.
Les protocoles de maintenance basés sur les données télématiques peuvent inclure :
- Des alertes automatiques pour les interventions de maintenance basées sur l'utilisation réelle
- Des recommandations de remplacement de pièces basées sur leur usure prévue
- Des ajustements dynamiques des intervalles de maintenance en fonction des conditions d'utilisation
- Des rapports détaillés sur l'efficacité et la consommation de carburant pour optimiser les performances
Cette approche data-driven de la maintenance permet non seulement de réduire les coûts d'entretien mais aussi d'augmenter significativement la disponibilité et la fiabilité des engins de chantier, contribuant ainsi à une meilleure productivité globale du chantier.
Formation des opérateurs aux techniques de conduite sécurisée
La formation des opérateurs est un pilier fondamental de la sécurité sur les chantiers. Même les engins les plus avancés et les mieux protégés ne peuvent garantir une sécurité optimale sans des opérateurs compétents et bien formés. Les techniques modernes de formation combinent théorie, pratique et technologies de pointe pour préparer les opérateurs à faire face à toutes les situations qu'ils pourraient rencontrer sur le terrain.
Simulateurs de conduite haute-fidélité pour entraînement en réalité virtuelle
Les simulateurs de conduite haute-fidélité représentent une avancée majeure dans la formation des opérateurs d'engins de chantier. Ces systèmes sophistiqués utilisent la réalité virtuelle (RV) pour créer des environnements de travail réalistes et immersifs, permettant aux stagiaires de s'entraîner dans des conditions proches de la
réalité. Ces simulateurs offrent plusieurs avantages clés pour la formation :- Sécurité : Les stagiaires peuvent s'exercer à des manœuvres dangereuses sans risque réel.
- Répétition : Les scénarios peuvent être répétés autant de fois que nécessaire pour maîtriser une compétence.
- Variété : Les simulateurs peuvent recréer une grande variété de conditions de travail et de situations d'urgence.
- Feedback immédiat : Les performances sont analysées en temps réel, permettant un apprentissage rapide.
Les simulateurs modernes sont capables de reproduire avec précision la physique des engins, les conditions météorologiques, et même les interactions avec d'autres machines ou travailleurs virtuels. Cette immersion permet aux stagiaires de développer non seulement leurs compétences techniques, mais aussi leur conscience situationnelle et leur capacité à prendre des décisions rapides en situation de stress.
Certification CACES R482 pour la conduite d'engins en sécurité
En France, la certification CACES (Certificat d'Aptitude à la Conduite En Sécurité) R482 est devenue la norme pour les opérateurs d'engins de chantier. Cette certification, qui remplace l'ancienne R372m depuis 2020, couvre une gamme plus large d'engins et met davantage l'accent sur la sécurité et les nouvelles technologies.
Le CACES R482 se divise en plusieurs catégories, chacune correspondant à un type spécifique d'engin. La formation comprend une partie théorique et une partie pratique, suivies d'examens rigoureux. Les points clés de la formation incluent :
- La réglementation et les responsabilités de l'opérateur
- La technologie et les caractéristiques des engins
- Les règles de sécurité sur le chantier
- Les techniques de conduite et de manœuvre sécurisées
- La maintenance de premier niveau
L'obtention du CACES R482 n'est pas seulement une exigence légale, c'est aussi un gage de professionnalisme et de sécurité pour les employeurs et les clients. La certification est valable 5 ans, après quoi un recyclage est nécessaire pour assurer que les compétences restent à jour avec l'évolution des technologies et des normes de sécurité.
Programmes de formation continue et mises à jour des compétences
La formation des opérateurs d'engins de chantier ne s'arrête pas à la certification initiale. L'évolution rapide des technologies et des réglementations nécessite une mise à jour continue des compétences. Les programmes de formation continue sont conçus pour maintenir et améliorer les compétences des opérateurs tout au long de leur carrière.
Ces programmes peuvent inclure :
- Des sessions de recyclage régulières sur les nouvelles réglementations et normes de sécurité
- Des formations spécifiques sur les nouvelles technologies d'engins
- Des ateliers pratiques sur l'optimisation de la productivité et de l'efficacité énergétique
- Des modules sur la gestion du stress et la prise de décision en situation d'urgence
De plus en plus, ces formations intègrent des éléments de e-learning et de réalité augmentée, permettant aux opérateurs de se former de manière flexible, sans nécessairement interrompre leur activité professionnelle. Par exemple, des applications mobiles peuvent fournir des rappels de sécurité quotidiens ou des quiz pour tester les connaissances.
La formation continue n'est pas seulement une obligation, c'est un investissement dans la sécurité, la productivité et la longévité des carrières des opérateurs.
En conclusion, la protection des engins de chantier contre les crashs et la destruction repose sur une approche multidimensionnelle. Des accessoires de protection robustes aux systèmes anti-collision avancés, en passant par le renforcement structurel et la maintenance préventive intelligente, chaque aspect contribue à créer un environnement de travail plus sûr et plus efficace. Cependant, la technologie seule ne suffit pas. La formation continue et le développement des compétences des opérateurs restent la clé de voûte de la sécurité sur les chantiers. En combinant ces éléments, l'industrie de la construction peut non seulement protéger ses précieux actifs matériels, mais aussi, et surtout, assurer la sécurité de son atout le plus important : son capital humain.